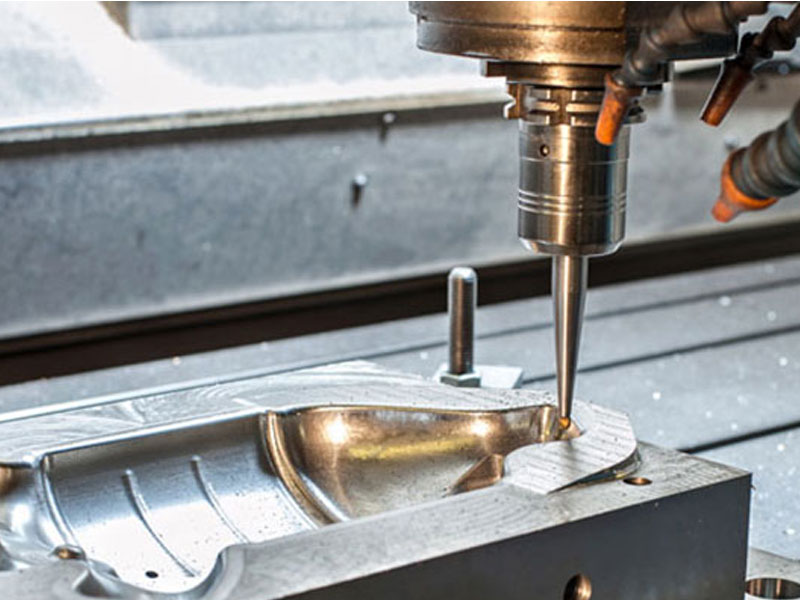
Diecasting begins with the creation of top-quality steel molds, also known as dies, which are designed to stand up to the extreme pressures and high temperatures that molten metal experiences. Dies are carefully designed to take in intricate details and maintain tight tolerances, and ensure that each part meets specific design requirements. In the process of casting, metals such as aluminum, magnesium, zinc, and copper are melted and then introduced into the die cavity in high-pressure. This quick injection, and its subsequent cooling creates parts which have excellent dimension stability as well as a smooth surface. Precision of the dies permits the production of components with complex geometries and shapes that would be impossible through other manufacturing methods.
One of the biggest advantages of diecasting is the ability to produce mass quantities. After the dies have been fabricated the dies can then be utilized to make thousands of similar components that have minimal variations. This high level of repeatability is essential for industries which require huge quantities of consistent parts. Diecasting is also known for its material efficiency. Diecasting produces minimal waste, as excess metal can be recycled and reused in subsequent casting cycles. It not only lowers cost of materials but also helps to promote sustainable manufacturing practices by minimizing resource consumption and waste. High manufacturing speed, accuracy, and material efficiency makes diecasting an attractive option in the quest to maximize their production processes.
Diecasting also offers considerable benefits in terms of the mechanical properties and performance. Parts made by diecasting are renowned for their durability and strength and dependability, both of which are vital features for parts used in challenging applications. Fine-grain formation that occurs when the metal is rapidly cooled the metal helps to create these excellent properties, which make diecast components suitable for use for high-stress conditions. Additionally, diecasting permits the use of thin walls and complex components without harming the strength of the finished product. This feature is particularly beneficial when it comes to aerospace and automotive industries, where weight reduction whilst maintaining strength and structural integrity can be crucial to boost fuel efficiency as well as overall efficiency. To get added details kindly look at Senadiecasting
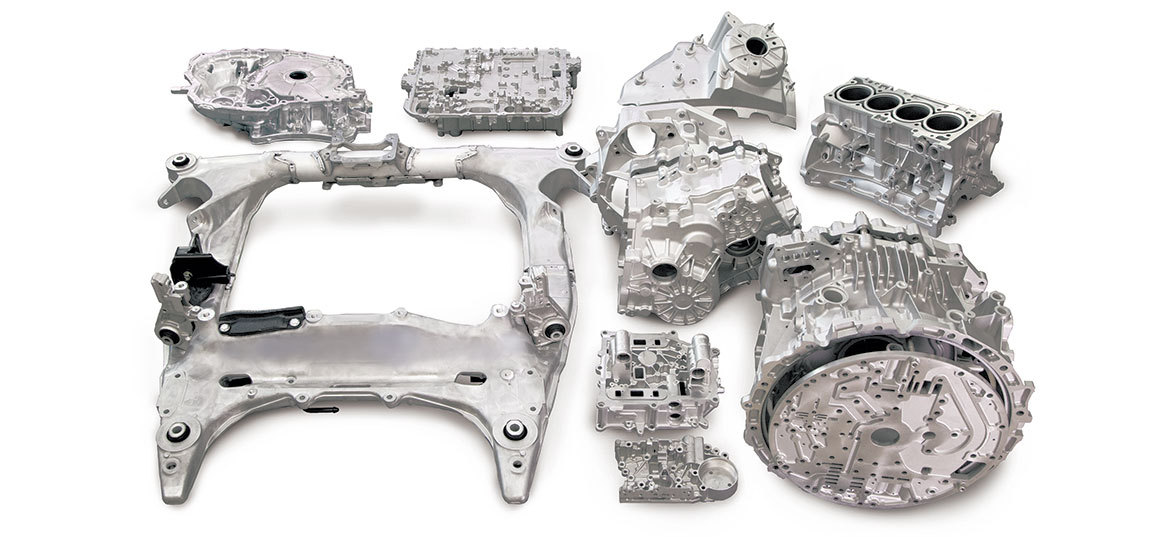
The materials you choose for diecasting significantly influences the properties and the performance of the finished product. Aluminium is an extremely popular material due to its outstanding strength-to-weight ratio, resistance to corrosion, along with its excellent electrical and thermal conductivity. Aluminum's properties make it ideal in aerospace and automotive industries where weight reduction is a major concern. Zinc alloys offer high strength and ductility. This makes them suitable for parts requiring fine detail and long-lasting. Magnesium alloys have the tiniest weight of metallic structural elements, offering advantages in areas where weight reductions are essential. Copper alloys, although utilized less often they are highly valued due to their excellent electrical conductivity as well as the resistance to corrosion. Each metal has unique advantages that allow manufacturers to choose the most suitable option to meet the specific requirements of their application.
Diecasting is a very efficient and versatile manufacturing process that is integral to producing intricate metal components with high precision and consistency. Its capacity to design parts with intricate details precise tolerances, perfect tolerances, as well as polished surfaces makes it an indispensable tool for all industries ranging from automotive and aerospace, to consumer electronics, as well as beyond. The use of different substances further expands the possibilities of diecasting. It allows companies to select the best alloy for their specific needs. As technology advances and the demand for high-quality, cost-effective components continues to grow and increase, diecasting will continue to be a critical process within the production process driving innovation and excellence in production.